Chemical reactions and smart actions: How digitalization succeeds in logistics
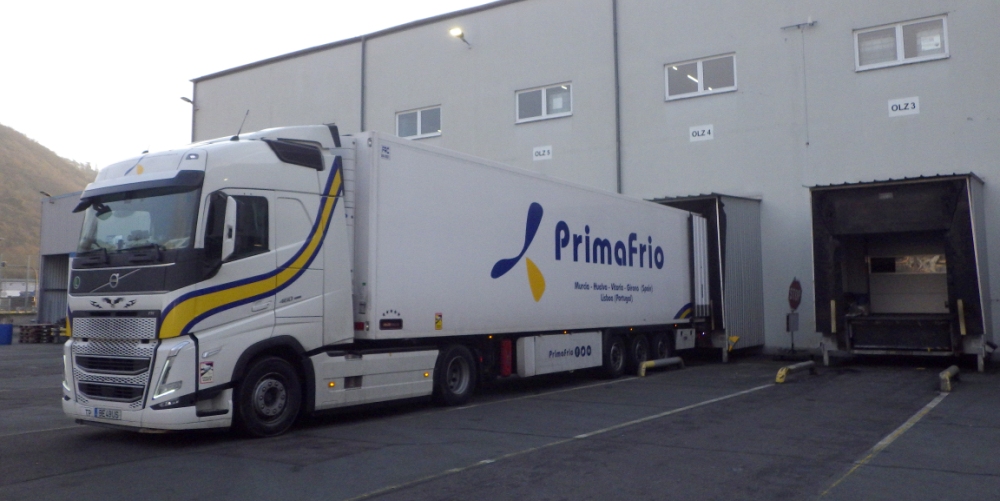
The chemical company Zschimmer & Schwarz has optimized its dock processes by implementing several solutions from Cargoclix (Photos: Zschimmer & Schwarz / private)
When existing systems no longer meet requirements, a clear vision and determined implementation are required. Henrik Schneider has proven just that. Within just a few months, as interim manager, he digitized processes at the chemical company Zschimmer & Schwarz with the help of a dedicated team and Cargoclix, thus laying the foundation for a sustainable digital future.
Freiburg i. Br., March 3, 2025. In December 2022, Henrik Schneider, owner of Schneider Consulting & Management for Logistics, took over as Interim Head of Logistics at the chemical company Zschimmer & Schwarz in Lahnstein. One of the challenges: an existing, but dysfunctional yard management system had not delivered the desired results. Instead of efficiency, there were long waiting times for trucks, and security checks were handled manually – a time-consuming and unsatisfactory situation. By the beginning of 2024, this situation was a thing of the past. With the help of Cargoclix, not only was modern time slot management introduced, but the foundation for lean, future-proof logistics was also laid.
Safety and efficiency in chemical logistics
As a chemical company, Zschimmer & Schwarz is subject to special safety requirements. Trucks are only allowed to enter the factory premises if they meet strict specifications: from the vehicle’s roadworthiness and tire condition to clear rules of conduct in the event of an alarm on the factory premises. It was clear to the company that without clear processes and structured communication with the drivers – many of whom come from abroad – such standards could not be implemented efficiently.
The first step was to replace the inadequate legacy system with Cargoclix’s cloud-based SLOT timeslot management system. SLOT enables delivery and pickup times to be digitally coordinated, which not only reduces waiting times but also increases planning reliability. But Schneider and the company’s project team went a step further: With the SAFE CHECK-IN module, security checks were digitized, among other things, and drivers were provided with special apps that enabled communication in the local language. Drivers can now access all relevant information and submit freight documents digitally upon delivery. Schneider was already familiar with the system from other companies and projects.
“Small steps are better than one big bang,” emphasizes the interim manager. The introduction of the new systems therefore took place in several phases. After the necessary processes had been defined in joint workshops, SLOT was first used to optimize truck delivery and pickup times. In the next step, the company integrated SAFE CHECK-IN to digitize security checks and integrate drivers more efficiently into the processes. In addition, QR codes, flyers, and touch terminals were installed to inform drivers about the use of the app and provide support when needed.
The language barrier was a particular challenge. Many drivers, especially those from Eastern Europe, had difficulty understanding the guidelines. However, with the app – which automatically translates conversations into all common languages, allowing drivers to respond in their native language – and additional support services, the majority of drivers were able to participate. For the remaining 30 percent, who still require personal assistance, targeted training was offered, and company employees took them by the hand and guided them through the processes.
Processes redefined and optimized
Digitalization was accompanied by comprehensive process optimization. Vehicles are now recorded with a unique Cargoclix ID and automatically assigned a ramp. This makes processes more predictable: Vehicles are guided across the site in a structured manner, loading processes are prepared at the ramp, and drivers are only allowed to move around accompanied – the process is completed within a few minutes. The integration of SLOT into the SAP ERP system will also enable, among other things, the automated creation of shipping documents in the future, which saves time and reduces errors, and ensures clear shipment and vehicle information for loading and unloading.
Another innovation was the integration of scales, which will be directly integrated into the digital workflow in the future. As soon as a vehicle passes the scale, the weight is automatically reported to the SAP system. In the future, the company plans to also provide transport documents via interfaces directly from SAP, for example, to further reduce paper consumption.
Booking a time slot costs just 50 cents – a small investment that Zschimmer & Schwarz deliberately makes for the transport companies without passing it on. “No one gets in at Zschimmer & Schwarz without a booked time slot,” Schneider explains. “The costs for the company are marginal with around 75 trucks per day, while the benefits are enormous. Ultimately, booking time slots leads to a significant increase in efficiency,” he emphasizes.
Digitalization as a strategic goal
The digitalization of logistics was not just a technical project, but also a strategic response to local challenges. In Lahnstein, a major construction site severely disrupted traffic. To ensure the flow of goods despite the closures, Zschimmer & Schwarz relied on real-time monitoring of arrival and departure times—a decisive advantage in critical situations with the ability to plan deliveries.
The company is also already thinking ahead: A shipment dashboard that tracks container shipments and informs customers about the exact delivery status is currently under development. This will not only increase internal efficiency but also improve customer communication.
Collaboration as the key to success
The success of the project was due in no small part to the close collaboration between Zschimmer & Schwarz, the service provider Cargoclix, and the employees. Meetings were held every two weeks to gather suggestions for improvement and feedback. The loading teams, in particular, provided important input from their daily work, which directly influenced the further development of the systems.
The entire project took approximately 14 months, with the integration of the SAP interface taking up the most time. With manageable investments in the actual system, the project was also extremely efficient from a cost perspective. “When progress becomes visible, the work is really enjoyable,” Schneider summarizes.
Digitalization with a clear focus
The example of Zschimmer & Schwarz impressively demonstrates that digitalization is far more than simply introducing new technologies. It requires well-thought-out processes, the active involvement of all stakeholders, and a step-by-step, strategic approach. With a clear focus on efficiency, security, and sustainability, the company demonstrates how digital transformation can be sustainably and successfully achieved.
“Digitalization not only reduces costs, it creates synergies and saves valuable time,” emphasizes Schneider. A carefully implemented project can not only help counteract the shortage of skilled workers, but also open up the possibility of redeploying existing staff to more value-added tasks. “It’s important to be aware that digitalization initially involves effort,” he emphasizes. “But it is essential for all companies that want to secure their future viability.”
About Zschimmer & Schwarz
Zschimmer & Schwarz is a global supplier of chemical auxiliaries and specialties with headquarters in Lahnstein near Koblenz. The company was founded in Chemnitz in 1894 and remains 100% family-owned to this day. For more than 130 years, Zschimmer & Schwarz has been offering specialty chemical solutions and, with seven business divisions, is positioned across industries. Customized chemical auxiliaries are developed, produced, and distributed for the leather, ceramics, textile, and chemical fiber industries. Customers around the world also trust the traditional company’s chemical specialties for the production of cleaning agents, personal care products, lubricants, and for industrial applications. The Zschimmer & Schwarz Group comprises 28 companies in 16 countries on five continents, 21 of which have their own production facilities.
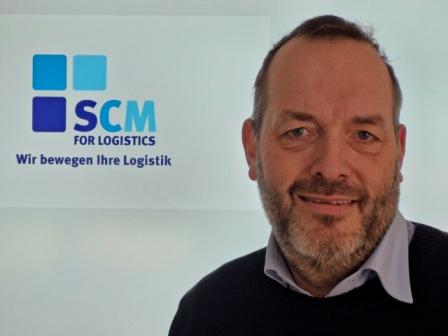
Henrik Schneider led the digitalization project. (Photos: Zschimmer & Schwarz / private)
About Zschimmer & Schwarz
Zschimmer & Schwarz is a global supplier of chemical auxiliaries and specialties with headquarters in Lahnstein near Koblenz. The company was founded in Chemnitz in 1894 and remains 100% family-owned to this day. For more than 130 years, Zschimmer & Schwarz has been offering specialty chemical solutions and, with seven business divisions, is positioned across industries. Customized chemical auxiliaries are developed, produced, and distributed for the leather, ceramics, textile, and chemical fiber industries. Customers around the world also trust the traditional company’s chemical specialties for the production of cleaning agents, personal care products, lubricants, and for industrial applications. The Zschimmer & Schwarz Group comprises 28 companies in 16 countries on five continents, 21 of which have their own production facilities.
CARGOCLIX SLOT
CARGOCLIX SLOT is a web-based time slot management system for optimizing loading and unloading processes at the dock. Consignees can set available loading times, and freight forwarders and carriers can book their preferred delivery times. All that’s needed for booking by freight forwarders and carriers is internet access.
Cost per slot booking: 50 cents. This fee is borne either by the booking company or, alternatively, by the consignee/location operator.
System description
- Interface to the ERP system or as a stand-alone solution
- Variable ramp opening times and flexible time window lengths depending on the number of pallets, tonnes, vehicle type, etc.
- Individual settings for break and vacation times, shift changes, booking limits, etc.
- Deposit of capacity limits such as personnel, forklifts or processing capacities
- Layouts and rights assignment for rebookings and changes
- Plausibility checks of booking data through duplicate checks, comparison of number ranges, etc.
- Event-based notifications and alerts
- Recording and evaluation of incoming goods flows with punctuality and processing times
- Real-time comparison of booked and unbooked time slots (requirement: ERP interface)
- Tracking of loading and unloading processes in real time with selectable screen display as schedule with ramp view, tabular booking list, traffic light system with color symbolism
- Recording of incoming goods flows with planned time/actual time per truck, quantity and quality per delivered shipment as well as comparison of delivered actual and target quantities from contracts
- KPI tool “CARGOCLIX Logistics Monitor” for controlling ramps using individual KPIs (Key Performance Indicators)
- “CARGOCLIX ETA App” for dynamic arrival time calculation at the ramp through intelligent calculation of the “Estimated Time of Arrival”.
- “CARGOCLIX TERMINAL” Realization of the “Gateway 4.0” without the use of personnel
About Cargoclix
Cargoclix is a leading provider of digital solutions in the transport and logistics sector. Cargoclix’s products enable end-to-end digital processes for yard and transport logistics and, with over 180,000 users, achieve one of the largest reach in the industry. All products are available as Software as a Service (SaaS) in the cloud and, thanks to their modular structure, offer flexible combination options that ensure complete digitalization and automation of logistics processes.
Cargoclix’s most well-known solutions include:
- Cargoclix SLOT: A modular, customizable software for optimizing processes at the ramp. SLOT is one of the most widely used products in the field of time slot management.
- Cargoclix SAFE CHECK-IN (SCI): A digital solution that efficiently connects truck drivers and logistics locations. It optimizes the entire check-in process and increases efficiency at logistics locations.
- Cargoclix WORKFLOW MANAGEMENT (WFM): A modular solution for the quick and easy digitalization and optimization of individual workflows in yard and transport logistics. It successfully helps reduce personnel costs and contributes to optimized workflows and error prevention through process automation.
- Cargoclix TENDER: A logistics platform for global tenders for transport by road, rail, air, sea, and inland waterways, as well as courier express parcel services and logistics services such as warehousing. With over 28,000 registered members from industry, trade, and freight forwarding, TENDER is one of the leading international tender platforms.
Cargoclix is a brand of Dr. Meier & Schmidt GmbH. The company was founded in 1998 and is headquartered in Freiburg im Breisgau. www.cargoclix.com
Follow Us on Social Media